Regulations such as ATEX, UKCA EX, DSEAR and NEC directly address safety hazards within your working environment. These hazards can include the handling and maintenance of potentially flammable, explosive, and thermally reactive dusts, gases, vapours, and other materials. If not properly controlled, these hazards could lead to potentially catastrophic fire and explosive risks. It is the asset owner/guardian’s responsibility to ensure they are compliant with the necessary regulations within their country of residence.
Our highly qualified engineers & process safety consultancy specialists use their expertise & site experience, coupled with access to an extensive library of both current & historical UK & international directives, standards, guidelines & legislation to deliver a range of Process Safety consultancy services across all industries & sites containing process safety issues.
The Process Safety division compliments our established engineering services: we offer a one-stop Process Safety service from supporting your initial plant design, to HAZOPs and other such studies (HAZOPs, HAZID, ATEX (DSEAR) assessments) through to determination of Hazardous Area Classification, associated equipment installation, maintenance, and inspection.
We do not only specify the Hazardous Area Classification for an area, but also the protection requirement and the suitability of equipment in, or to be placed in, that hazardous area. Naturally, we also undertake ‘normal’ (non-hazardous) electrical and non-electrical equipment specification, installation, inspection, and maintenance which can all be included in our ‘one-stop’ service.
Our team (through from Process Safety Consultancy experts to Electrical Engineers) has the experience necessary to be able to recommend actions based on reasonably practicability and to ensure that the advice offered not only solves the safety problem raised but does so in a cost-effective way. A ‘pragmatic’ solution is what our team aim for. Real-life solutions for real-life problems.
Dependant upon the asset in question some of these assessments can be desktop based, although for a suitable and sufficient risk assessment, the environs of the area should really be a part of the study, hence on-site risk assessments are always a preference, although we appreciate this cannot always be the case.

PROCESS SAFETY CONSULTANCY ATEX/DSEAR Assessments
Gap Analysis – a review of where your site is, compared to acceptable situations, what should be improved and at what priority level?
ATEX/DSEAR ASSESSMENTS – HAVE YOU HAD ONE DONE? DO YOU NEED ONE?
It has to be remembered that DSEAR applies to all companies (with certain exceptions – mainly ‘ships’). If you are a small company, the assessment may be as simple as a short note on a piece of paper. If you are smaller still, there is no requirement to record the significant findings [DSEAR Regulation 5 (4) ‘Where the employer employs five or more employees, the employer shall record the significant findings of the risk assessment as soon as is practicable after that assessment is made…’]
However, for process safety auditing purposes, we would still advocate that a written report – of a suitable and sufficient format – is produced for your site. How can anyone check if the assessment has been done thoroughly without something to check?
IS IT UP TO DATE?
There is no strict ‘review date’, but every three years or when there is a ‘substantial’ change is advised. Is yours up to date? Does your process safety need auditing or reviewing?
DO YOU HAVE A BASIS OF SAFETY DEFINITION FOR EACH OF YOUR PROCESS ‘UNIT OPERATIONS’?
In other words, what, if it changed, could lead to a dangerous situation?
ELECTROSTATIC IGNITION SOURCE ASSESSMENTS.
There are thirteen recognised ignition sources. However, electrostatics are probably the least understood of them all and hence least controlled. Do you know the difference between a brush discharge and a propagating brush discharge? What Dust vent explosion relief calculations where explosion relief is provided. This is to show whether the surface area of an explosion relief panel is suitable for the silo/vessel that the material is stored in.
VAPOUR EVAPORATION CALCULATIONS
Vapour evaporation calculations, to cover pool spillages etc., which will show how long it takes for a spillage of a highly flammable liquid to evaporate to a safe concentration.
MATERIAL LABORATORY TESTING (EXPLOSION AND FLAMMABILITY TESTS)
Are you aware of the properties of your materials? Do you require more information to determine the appropriate Basis of Safety? Explosion suppression and explosion relief both require certain parameters of the material stored. Have you got the right data? Is the explosion relief designed for a different material and therefore may not work?
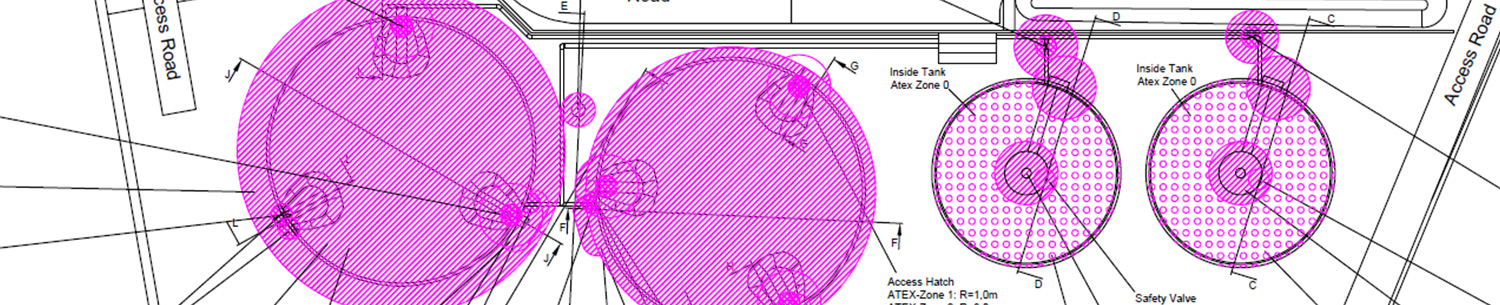
PROCESS SAFETY CONSULTANCY Hazardous Area Classification
Hazardous area classification is a probability assessment. What is the probability of a flammable atmosphere occurring at a particular location? It can be thought of as one of four:
- All the time
- Normally
- Rarely
- Never
These probabilities are then given ‘zones’ to classify them. Unfortunately, the zones do not match the above numbering system, but the equipment in those zones does:
Probability | Probability ‘number’ from above | Zone: (0, 1, 2 for gases & vapours; 20, 21, 22 for dusts/powders) 1 | Equipment category 2 |
---|---|---|---|
All the time | 1 | 0/20 | 1 |
Normally | 2 | 1/21 | 2 |
Rarely | 3 | 2/22 | 3 |
Never | 4 | None | None |
¹ I.e., zone plus one ² I.e., equipment category minus one
Are your production and storage areas, where flammable materials are, or may be, stored and/or used, so defined? If not, is an assessment required?
HAZARDOUS AREA CLASSIFICATION DRAWINGS
Have you got appropriate drawings and if so, do they also include the Temperature Class and Gas Groups required (where applicable)?
Do you show both plan and elevation? Do markings/signs on the plant reflect the drawings?
If not, we can produce the HAC drawings, or even update existing ones if required.
Explosion Protection Documentation (EPD)
In the UK, the Dangerous Substances and Explosive Atmospheres Regulations 2002 assessment is considered to be equivalent to an EPD, but in Europe, an EPD is an actual requirement – unless the local legislation specifically states otherwise. Basically, it can be considered to be a ‘Health and Safety Policy Document for the Prevention of Fires and Explosions’. Does it need reviewing, updating? Does it include all appropriate elements? Training, maintenance, permits, etc.?
Ignition Risk Assessments
Where existing electrical and non-electrical equipment is in a hazardous area, do they need a full electrical- and a non-electrical equipment ignition risk assessment to verify their suitability in the zones identified?
READ MORELab Testing
We have access to some of the best globally accredited lab testing facilities that are able to generate data on the flammability, explosivity and thermal reactivity of your substances such as dusts, gas vapours and chemicals.
READ MOREExpert Witness / Incident Investigation
Our team can be relied upon to deliver independent and impartial advice as the legal system requires as well as investigation findings.
READ MORE